|
Kerox Polyester Pigments |
These
are dispersions of inorganic and organic compounds in a special
grade of unsaturated polyester resin vehicle, which cross links
during curing with commercial grades of Gelcoat and GP resin
systems. |
Opaque and Translucent Pigments
are two varieties in this range. |
|
Kerox Epoxy
Pigments |
These are
dispersions of inorganic and organic compounds in a special
grade of saturated polyester resin vehicle, which functions
as a plasticizer in commercial grades of Epoxy resin
systems. |
Commercial
epoxy resin systems vary between manufactures and hence the
amount of hardener required to cure the resin (Amine
Equivalent Weight) varies. Addition of any third component
that is epoxy based will require the correct computation of
the hardener required. Usage of Kerox Epoxy Pigments
eliminates the need to make such computations. |
|
Pigment Usage
Levels |
The
following is the recommended usage level of Kerox Pigments
with commercial grades of molding resins. The percentage
levels listed here is based on the weight of the molding
resin. |
|
8%-12% |
Gelcoats |
|
|
4%-6% |
Laminates |
|
|
8%-10% |
Sheet/Dough Molding Compounds |
|
|
1%-5% |
Translucent
Pigments Usage |
|
|
4%-6% |
Filled Castings |
|
|
8%-10% |
Pultrusions |
|
|
Not
using enough pigments may lead to non-uniformity of color
and other surface defects. Higher pigmentation levels will
provide better color uniformity, color depth, brightness and
longer durability. |
|
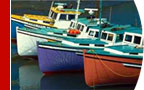 |
Mixing
Instructions |
Kerox Pigments mix readily with commercial polyester and
epoxy resin systems. Small quantities of pigments can be
mixed easily by hand stirring. However, for large
quantities of pigment, power mixing is necessary. The
following guideline is helpful for mixing Kerox Pigments
with resins: |
 |
Add a
weighed quantity of the pigment into a mixing container,
followed by a small amount of the resin. |
|
 |
The contents
are mixed well until the color is uniform. |
|
 |
This is
followed by adding the remainder of the resin, with
further mixing, until the system is homogeneous in
color. |
|
|
On
no account should a small quantity of the pigment be added
to a large bulk of the resin, without first thinning, as
described above. |
|
Catalyst and
Accelerator Addition |
The
catalyst for curing the pigmented resin should be added as
per the instructions of the original manufacturer of the
resin. As a general working rule the catalyst should be
added to the pigmented resin just before actual usage.
For best performance Kerox ME-50 MEKP Catalyst and Kerox
C-20 Accelerator should be used. A recommended usage
level is 3% on the weight of the resin of each. |
|
Storage
Stability |
Kerox Pigments have excellent stability in storage and the
minimum guaranteed shelf-life is 6 months. Storage below
250 0C is
recommended for longer shelf life. |
|
Color Matching |
Kerox Pigments can be mixed with one another to obtain
intermediate shades. Dark shades present no particular
color matching problems, but light shades may pose some
difficulty. Kerox uses the latest state-of-the art color
matching computer software and tools. Colors can be custom
matched to customer's requirements, provided the minimum
quantity is over 250 Kilograms. |
|
Contact
keroxoffice@kerox.org for sales or technical
assistance on our Polyester and Epoxy Pigment products.
|
|
|
|
Color Chart |
View over 400 colors
online. |
|
Literature and
Links |
|
|
 |
Value
Proposition |
Premium
Pigments: Quality inorganic and organic pigments from ISO certified
companies, conforming to the Color Index (C.I.) standards,
are used in the formulation of the dispersion. |
Engineered
Resin: We manufacture our own pigment grade resin, which
has been engineered in-house,
and which has evolved since 1968. |
Compatibility: This base
vehicle offers excellent compatibility with commercial
grades of polyester resin. |
Superior
Cross Linking: The unsaturated
pigment grade resin in our Polyester Pigments cross links during curing and provides
better structural properties to the composite. |
Flexibility: The chain length
of the pigment grade resin is designed to provide
flexibility in the polymer, thereby preventing surface
brittleness of the finished composite. |
Micron
Particles: The pigment
particles are processed to attain a particle size below 7
microns. |
Dispersion
Stability: The particles are dispersed and stabilized
using specially formulated surface active agents, using
science based on the DLVO concept. |
Maximum Loading
and Hiding Power: Our formulations contain the maximum
loading of dry inorganic and organic colors in the pigment
dispersion, thereby giving maximum coverage and hiding
power. |
Color
Uniformity: Provides a uniform surface coloration and
streak-free appearance in the finished composite. |
Color
Consistency: Computerized color analysis laboratory
using spectrophotometers enables color consistency between
batches. |
ISO
Procedures:
Processing is done as per ISO 9001:2002 procedures, ensuring
optimium quality control. |
Cost:
Kerox Pigments offer the lowest cost of coloring unit
surface area of the finished composite |
|
|
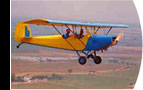 |
Product
Applications |
Kerox Pigments have been widely
used since 1968 in manufacturing processes such as Hand
Lay-Up, Spray Lay-Up, SMC, DMC, Pultrusion, Filament
Winding, Vacuum Bagging, RTM, and RFI. It has served
to color the products of numerous industry segments. |
Building Industry - Structural frames and bridges, doors
and windows, flooring and tiles, table top laminates,
bathtubs and jacuzzi, bathroom accessories and fittings,
roof sheets, ladders, fences, mobile dwellings, portable
toilets, and water tanks. |
Marine Industry - Boats and ship construction, decks, and
masts. |
Aerospace and Automotive - Aircraft bodies and structural
frames, wings, helicopter blades, space equipment, rocket
bodies, missile housing, car bodies, fenders, and canopies. |
Sports - Surf boards, skis, protective gear and helmets,
fishing rods, goal posts, and flag masts. |
Medical - Prosthetics (artificial limbs) |
Chemical Industry - Process plant equipment, pressure
vessels and containers, tanks, cooling towers. |
Electrical Industry - Switch boxes, electrical housings, and
electric poles. |
Recreational - Amusement park facades and equipment, roof
lights, sculptures, specialty furniture, and architectural
items. |
|
|
|
|
Certified
Quality |
Kerox has been
awarded the ISO 9001:2000 certification by UKAS (UK) and
ANSI-RAB (USA) for the manufacture of Polyester and Epoxy
Pigments. |
|
Super
Range Pigments |
Kerox has
introduced this exciting range of high quality and low cost
product. These pigments have the same loading,
coverage, hiding power, as our Premium Range products. |
To make it
convenient for our customers the Premium Range uses our
existing numbering system and is reflected in our online
color chart. This range is manufactured using the time
tested and evolved formulae since 1968. |
The newly
introduced Super Range also uses the same numbering as the
Premium Range, except that a suffix -S is attached.
Most of the colors in our standard list of Premium Range
Pigments are available in the equivalent Super Range.
Color variations between the Premium and Super Ranges is
typically ΔE ≤ 2. |
Super Range
Pigments have a lower cost than our Premium Range Pigments
because of sourcing choices in raw materials and
technological innovations made possible by our R&D. |
The choice of
selecting between the Premium and Super Range of Pigments is
left to the discretion of the customer. Both are high
quality products. |
|
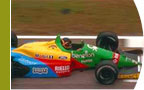 |
Superior Performance |
Light Fastness:
Kerox Pigments exhibit excellent light fastness and will not
fade or discolor on exposure to sunlight. However,
pastel shades in our range are recommended for indoor
applications. |
UV Resistance:
Ultraviolet (UV) radiation, from sunlight,
accelerates the chemical and physical degradation of FRP
moldings exposed to outdoor conditions. The
degradation occurs mostly on the surface of the molding.
But once degraded, the surface tends to chalk and erode due
to weathering, exposing fresh surface to further attack.
Protection of outdoor structures fabricated in FRP is,
therefore, important. Kerox Pigments absorb and
convert UV radiation into heat, which is dissipated to the
surrounding medium readily. Therefore, pigments
prolong the outdoor service life of composite moldings.
Protection by this mechanism depends on the pigment
concentration on the surface. Gel coats having higher
pigment loading will, therefore, afford longer protection. |
Outdoor Durability:
The durability of the Kerox Pigments depend on environmental
conditions such as heat, light, moisture, and industrial
pollutants present in the atmosphere. Generally the
darker shades will have better durability when exposed to
outdoor conditions. |
Heat Resistance:
FRP moldings manufactured using dough/sheet molding
compounds are usually processes at elevated temperatures of
140 0C to 160
0C, or higher. The heat resistance of the
pigments in such applications depend on exposure time,
temperature, oxidizing conditions during processing, heat
transfer coefficients, and heat transport rates. We
supply special polyester pigments for coloring these
moldings. |
Chemical Resistance:
The
compatibility of pigments to chemicals depends on the
material constitution of the pigments themselves. As a
general rule chemicals that would react with polyester
resins would be incompatible with the pigments. Our
technical staff would be able to assist you in recommending
the available choice of colors for your applications. |
Electrical Properties:
Polyester moldings are
used to a large extent in electrical applications.
Special Kerox Pigments can be offered which will have no
adverse effects on track resistance, surface resistivity,
dielectric strength and other insulation properties. |
Toxicity: The toxicity of Pigments
depends on the raw materials used in the formulation.
We can recommend a choice of pigments depending on your
requirements. |
|
Epoxy Pigments |
Epoxy Resins have poor color
stability and tend to darken upon hardening.
Therefore, usage levels of light colored Pigments will be
higher than that for dark colored Pigments. Sample
testing is recommended with epoxies. |
|